What is the impact of automation in the industrial sterilisation process for pharmaceutical drugs or medical devices manufacturing? The automation of a sterilisation plant can concern a broad range of tasks, from the process of stacking, transport and loading to the steriliser, as well as the subsequent unloading.
It is proven that the integration of an automated system, in fact, increases performance and productivity up to 40% in the overall production process and provides an average reduction of 15% of the duration of some sterilisation cycles, in addition of energy consumption savings of up to 20%.
Similar patterns hold on for other pharmaceutical manufacturing processes such as freeze-drying, among others. Are those all advantages? This article analyses the role of manual and automatised process within a manufacturing process and why robotic and automation technologies will eventually become a key factor of profitability, particularly in terms of productivity and safety.
Trends in a pandemic
The pharmaceutical industry is experiencing a substantial surge in automation, a momentum that has been significantly amplified by the COVID pandemic which started in 2020. The pandemic has acted as a catalyst, emphasising the criticality of these initiatives and, in turn, expediting the adoption of automation and digital solutions to enhance pharmaceutical research, development, and manufacturing processes.
The level of automation in the pharmaceutical industry varies according to specific applications and the diverse practices adopted by companies and countries.
The initial expenses associated with implementing robotic systems can be considerable
While human labour remains crucial in the pharmaceutical industry for a multitude of tasks, it is important to acknowledge that it comes with certain drawbacks and challenges. Here are some of the disadvantages of relying on manual operations in this sector.
Human error: One of the most significant drawbacks is the potential for human error. Mistakes in tasks like data entry, manufacturing, and quality control can have severe consequences, including the production of substandard or unsafe drugs. Consequently, stringent quality control measures and thorough audits are imperative. In this context, automation emerges as a promising solution for error reduction.
Speed and efficiency: Automated systems can outperform humans in certain tasks, resulting in shorter production times and potentially preventing delays in product availability. For instance, in the case of sterilising large-volume parenteral, manual loading and unloading of the product into the autoclave can extend the production cycle due to the time needed for the chamber to heat up and cool down, as well as for operators to enter. In this case, an automated process could amount to a time savings of more than one hour for each sterilisation cycle in certain cases.
Automated product handling systems in high-capacity pharmaceutical sterilisation systems increases performance and productivity up to 40% in the overall production process. A robotised processing integrated in a sterilisation system enables to prepare the product arriving from one or more filling lines, as packaged material (bags, bottles or PFS) which have been previously automatically classified and placed on the transport conveyors, to be loaded directly into the steriliser chamber without any human intervention. In addition to covering whole operational phases, connecting the sterilisation process from the filling line to the inspection line.
Unlike the manual loading and unloading process, which requires the product through an extended cooling phase to reach a temperature permitting the manual handling of the product, the fully automated process enables to unload at higher temperature providing higher efficiency with an average reduction of 15% of the duration of the sterilisation cycle thus saving up to 20% in energy consumption.
Labour costs are a factor that represents a substantial share of the total expenses in the pharmaceutical industry
Health and safety risks: Working with certain pharmaceutical materials and processes can pose health and safety risks to employees. Ensuring the safety of workers requires additional resources and precautions.
Sterilisation of medical devices plays a critical role in ensuring patient safety by eliminating harmful microorganisms. One widely used method is sterilisation with ethylene oxide gas, a process known for its effectiveness in penetrating various materials and complex device designs.
Ethylene oxide is a highly effective sterilisation agent, but it is not without its concerns, primarily related to toxicity. The Occupational Safety and Health Administration (OSHA) and the Environmental Protection Agency (EPA) in the United States have established stringent regulations to safeguard workers and the environment during its use. In some cases, the current process operating in ethylene oxide factories is still manual or partially automated. This means that there are operators on the shopfloor who are at risk of EtO exposure.
To address this concern, comprehensive end-to-end automation solutions have been implemented, spanning from warehouse operations to every stage of the sterilisation process. These systems are designed to minimise human exposure to ethylene oxide gas, thus enhancing safety in the work environment, in addition to enhancing the overall process efficiency.
An automated sterilisation line includes preconditioning, sterilisation, and aeration stages, with an automatic loading/unloading system to streamline material transfer.
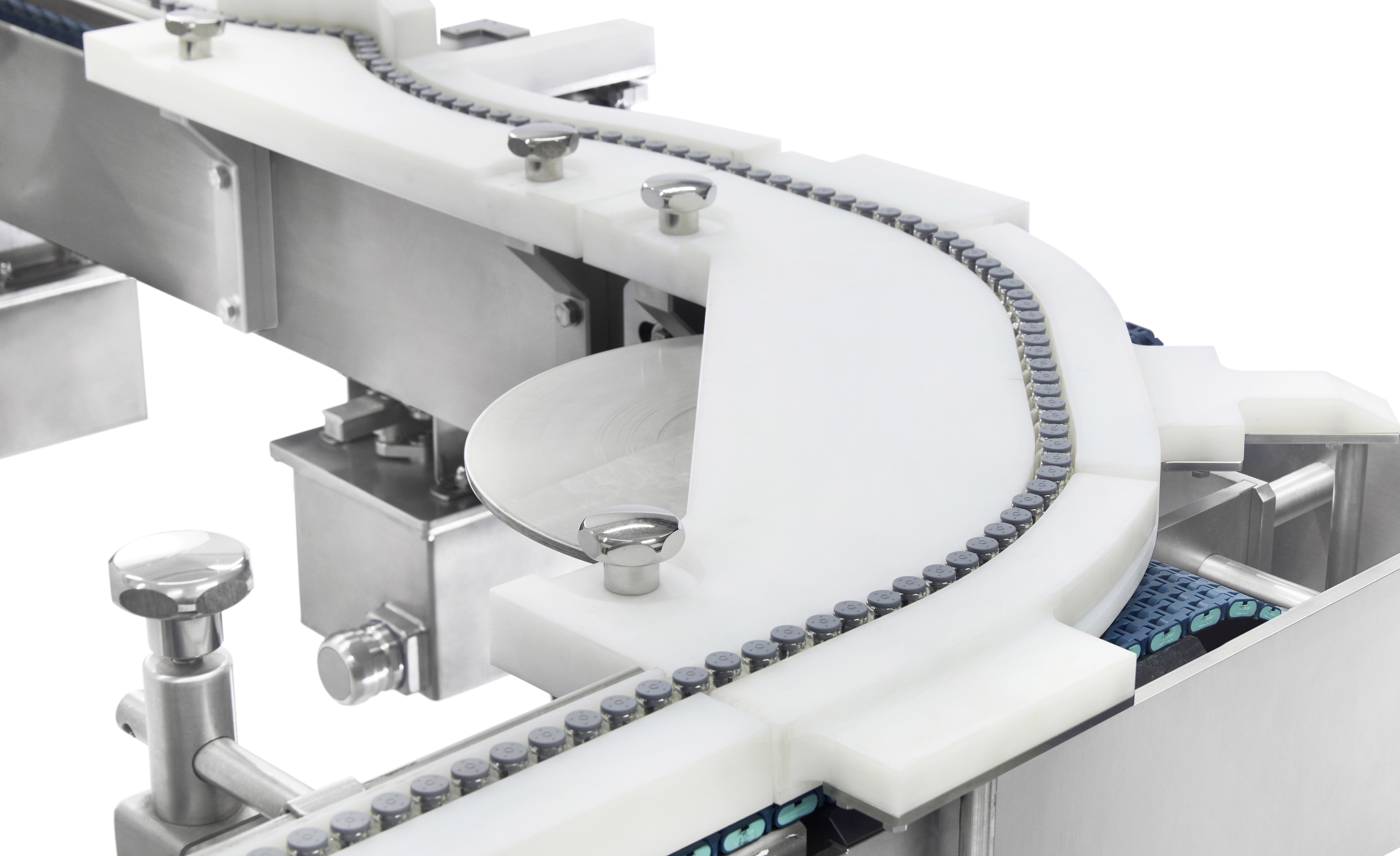
Monotony and repetition: Some pharmaceutical tasks can be highly repetitive and monotonous, which can lead to employee fatigue, reduced job satisfaction, and a higher likelihood of errors.
A clear illustration of this would be in the way bottles, bags or prefilled syringes are handled before undergoing the sterilisation process. These medical containers are methodically arranged on the tray to maximise capacity and ensure a proper sterilisation process.
To address these challenges, custom-designed robotic solutions are being employed to replace human labour. These robots not only enhance the speed of the process but also ensure consistent repeatability, thus mitigating the risks associated with manual handling and promoting greater efficiency in pharmaceutical operations.
If a format change is required, robot grippers can be easily replaced to minimise downtime.
Scalability: The pharmaceutical industry often faces the difficulty of increasing production to keep up with rising demand. Unlike automated processes, hiring and training more staff can be slower and expensive. This is why there is a growing demand for flexible automation solutions to handle various tasks or product formats more efficiently.
An example to illustrate it, particularly striking in the freeze-drying process, is a novel vial transportation system that utilises a mobile platform configured to adapt to a wide range of vials during the loading and unloading processes of lyophilisers. This solution enables a reduction in manual operations within the aseptic area while also contributing to reducing the risks of cross-contamination during pharmaceutical product manufacturing. The multiple formats that previously needed manual changes can now be replaced by a single device designed to automatically adjust to the vial's diameter, without the need to interrupt the containment or isolation process, ensuring the sterility level without repeating the cleaning or decontamination process for each different format in every cycle.
Moreover, these systems are commonly incorporated with prior stages, including filling lines and sterilisation tunnels.
Labour costs: Finally, but not less important, labour costs are a factor that represents a substantial share of the total expenses in the pharmaceutical industry. Wages, benefits, and regulatory obligations related to labour have a significant impact on production costs. Managing a sizable workforce, encompassing recruitment, training, and staff retention, can be both resource-draining and time-consuming.
Meanwhile, the initial expenses associated with implementing robotic systems can be considerable. This encompasses the costs of procuring, installing, and programming the robots, alongside the investments required to train the workforce in robot operation and maintenance. In certain countries, companies might delay automation efforts due to government subsidies that incentivise labour-intensive practices.
Conclusions
While there are compelling reasons for automation, there can also be reservations when it comes to implementing automated solutions. The complexity of this issue does not solely hinge on the technology, as previously exemplified, but also on the intricate process of integration.
Consequently, the pharmaceutical and medical device industry is increasingly seeking suppliers capable of delivering comprehensive end-to-end solutions that guarantee both quality and on-time project execution.
By tackling these challenges, the sector can better manage the complexity of integrated projects, ensuring the efficient and dependable delivery of essential products to society.